Pharmaceutical Product Filling Machines
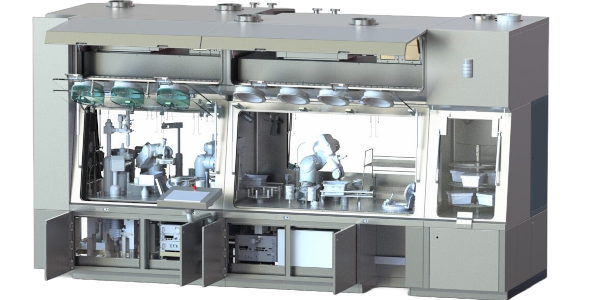
In the pharmaceutical sector, efficiency and precision are paramount. Filling machines play a crucial role in achieving these objectives.
We’re going to take a closer look at the different aspects of filling pharmaceutical products and the central role played by machines in this process.
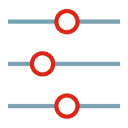
Customised Technical Solution
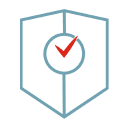
Static and Dynamic Protection
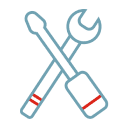
Rapid Installation and Implementation
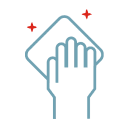
Easy-to-clean Surface
Would you like an estimate for your project?
Don't hesitate to contact us for a personalised quote.
They Trust Us
Filling Machines: a Necessity for the Pharmaceutical Industry
The pharmaceutical industry is a sector where accuracy and precision are fundamental requirements. To achieve this, companies use filling machines. These ensure the precise, controlled distribution of liquids into various types of container, such as vials and bottles.
Automated filling machines guarantee compliance with safety and quality standards, while maximising productivity and efficiency. They are therefore an essential component of the pharmaceutical production system.
Different Types of Filling Machine
There are several types of filling machine, depending on the nature of the product to be packaged and the type of container. The main types are volumetric fillers, weight fillers, constant level fillers and vacuum fillers.
Volumetric fillers are ideal for non-viscous liquids and low-viscosity products. Weight fillers, on the other hand, are ideal for high-viscosity products. Constant level fillers allow each container to be filled to the same level, whatever the quantity of product. Finally, vacuum fillers are used for foaming products.
Importance of the Capsule System in Filling
The capsule system is an essential component of the filling machine. It enables the containers to be closed securely after filling. This system is particularly crucial in the pharmaceutical sector, where product integrity must be preserved at all costs.
There are different types of cap systems, such as screw cap, pressure cap, heat seal, and so on. The choice of capsule system depends largely on the type of container and the nature of the product.
Production Line and Packaging: Two Key Stages
The production line and packaging are two essential stages in the filling process. The production line covers all stages, from the filling process to final packaging of the product. It must be designed to optimise efficiency and productivity while guaranteeing product quality.
Packaging is the final stage in the filling process. It must protect the product from damage and contamination, while providing an attractive presentation for the consumer. It is therefore crucial to choose the right packaging system, capable of meeting the specific requirements of the pharmaceutical industry.
In short, the filling process in the pharmaceutical industry is a complex task that requires specialised machinery. The choice of these machines is crucial and must be based on a number of criteria, such as the nature of the product, the type of container, production capacity, etc. Comparators can be a great help in this selection process, as can a thorough understanding of the role of cap systems and the importance of the production line and packaging.
Criteria for Selecting a Filling Machine
Choosing a filling machine in the pharmaceutical industry is not a simple task. Several factors need to be taken into account, including the nature of the product, the type and size of container, and the desired production capacity.
Each type of product and multiple containers requires specific considerations. For example, filling liquid products may require a different machine model to filling capsules. The speed or output of the machine is also a crucial factor, as it has a direct impact on production capacity.
Optimising the Filling Process
Optimising the filling process in the pharmaceutical industry is crucial. It ensures the efficiency and productivity of the production line, while guaranteeing the quality and integrity of the product.
The filling system is an important aspect of this process. It includes the filling machine, the capping system and the packaging system. Each element must work in harmony to ensure a smooth and efficient process.
The filling machine ensures precise, controlled distribution of the product into different types of container. The capping system seals the containers securely after filling. The packaging system protects the product from damage and contamination, while providing an attractive presentation for the consumer.
Optimising the filling process also involves choosing the right filling machine. This choice depends on a number of factors, including the nature of the product, the type and size of container and the desired production capacity.
The Importance of After-sales Service
After-sales service is a critical aspect of choosing a filling machine for the pharmaceutical industry. Good after-sales service ensures that the machine continues to operate at optimum levels, maintaining a high level of production efficiency.
Services can include regular maintenance, repair services and even operator training. These services ensure that the machine is always in good working order and that any potential problems are quickly identified and resolved to avoid any disruption to the production process.
An efficient after-sales service can also provide advice and recommendations on how to optimise the use of the machine, according to the specific needs and requirements of the pharmaceutical company.
In conclusion, the filling process in the pharmaceutical industry is a complex task that requires specialised machinery. The choice of these machines is crucial and must be based on a number of factors, including the nature of the product, the type of container, production capacity and the quality of after-sales services. Comparators can be a great help in this selection process, as can a good understanding of the filling process.
Need a specific configuration? Customised dimensions?
Discover our insulators, tailor-made to meet your requirements.